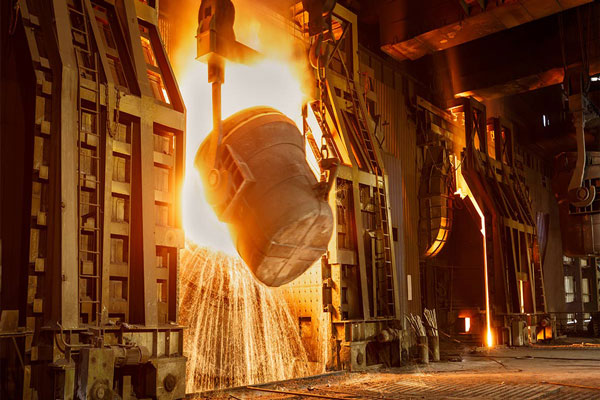
۱۷ اردیبهشت داستان فولاد ازدیروز تا امروز
فولاد یا پولاد (به انگلیسی: Steel) آلیاژی از آهن است که بین ۰٫۰۰۲ تا ۲٫۱ درصد جرم آن کربن است. خواص فولاد به کمک تغییر در درصد کربن، عناصر آلیاژی و عملیات حرارتی قابل کنترل است. استفاده از فولاد به دلیل استحکام کشش نهایی زیاد و قیمت نسبتاً پایین آن در ساخت صنایع مختلفی از قبیل ساختمان سازی، سازههای زیرساختی، ابزارها، کشتیها، پلها قطارها، خودروها، ماشین آلات، تجهیزات و سلاحهای نظامی کاربرد گسترده دارد.
امروزه برای تولید فولاد (fe3c) از روشهای نوینی مانند، فولادسازی به روش اکسیژن قلیایی (BOf)، استفاده میشود که علاوه بر کاهش قیمتها، منجر به افزایش خلوص فولاد تولیدی نیز گردیدهاست. فولاد یکی از بیشترین مواد تولید شده توسط انسان است و سالانه تقریباً بیش از ۱٫۶ میلیارد تن فولاد در سراسر جهان تولید میشود.
استحکام فولاد با «میزان کربن محلول» به شدت افزایش مییابد اما از طرفی این افزایش استحکام باعث کاهش قابلیت جوشکاری و افزایش احتمال شکست ترد میشود. استحکام فولادهای فریتی (فِرومغناطیس) رابطه معکوسی با شکلپذیری دارد. تلفیق استحکام و شکلپذیری با پایدارسازی فاز آستنیت (پارامغناطیس) در فولادهای مدرن چند فازی قابل بهبود است
خواص فولاد
حتی در محدوده کوچکی از غلظتهای مخلوط آهن و کربن که فولاد را میسازند، چندین ساختار متالورژیکی مختلف با خواص بسیار متفاوت میتوانند تشکیل شوند. درک چنین خواصی برای ساخت فولاد با کیفیت ضروری است. در دمای اتاق، پایدارترین شکل آهن خالص، ساختار (BCC) به نام آهن آلفا (α) است. این فلز نسبتاً نرم میتواند تنها غلظت کمی از کربن را در خود حل کند. ((حداکثر ۰٫۰۰۵٪ در دمای صفر درجه سانتیگراد و ۰٫۰۲۱٪ (درصد وزنی) در دمای ۷۲۳ درجه سانتیگراد))
افزودن کربن در آهن آلفا سبب ایجاد فریت میشود. در دمای ۹۱۰ درجه سانتیگراد، آهن خالص به ساختار مکعبی (FCC)، که به آن آهن گاما (γ) میگویند، تبدیل میشود. افزودن کربن در آهن گاما، موجب ایجاد آستنیت میشود. ساختار بازتر آستنیت (که FCC است) باعث میشود قابلیت انحلال ۲٫۱٪ کربن در دمای ۱۱۴۸ درجه سانتیگراد را داشته باشد. این میزان ۳۸ برابر میزان کربن موجود در فریت است که نشاندهنده محتوای کربن بالای فولاد است که چدن نامیده میشود. هنگامی که کربن با آهن از محلول خارج میشود، ماده بسیار سخت اما شکننده به نام سمنتیت (Fe3C) تولید میشود.هنگامی که فولادهایی با کربن دقیقاً ۰٫۸ درصد (معروف به فولاد یوتکتوئید) سرد میشوند، فاز آستنیتی (FCC) مخلوط تلاش میکند تا به فاز فریت (BCC) بازگردد. در این صورت، کربن دیگر در ساختار آستنیت (FCC) جای نمیگیرد و در نتیجه کربن اضافی ایجاد میشود. یکی از راههای خارج شدن کربن از آستنیت این است که کربن از محلول به صورت سمنتیت رسوب ایجاد کند تا فاز اطراف آهن BCC بهنام فریت با درصد کمی کربن در محلول باقی بماند. فریت و سمنتیت، بهطور همزمان رسوب میکنند و ساختار لایهای به نام پریت را تولید میکنند که به دلیل شباهت آن به صدف مروارید نامگذاری شدهاست. در ترکیب هایپریوتکتوئیدی (بیش از ۰٫۸٪ کربن)، کربن ابتدا به صورت ناخالصی (آخال)های بزرگ سمنتیت در مرز دانه آستنیت رسوب میکند تا زمانی که درصد کربن موجود در دانهها به ترکیب یوتکتوئیدی (کربن ۰٫۸٪) کاهش یابد، که در آن نقطه ساختار پرلیت را تشکیل میدهد. برای فولادهایی که کمتر از ۰٫۸٪ کربن دارند (هیپو یوتکتوئید)، فریت ابتدا در دانهها تشکیل میشود تا زمانی که ترکیب باقیمانده به ۰٫۸٪ کربن برسد، در این مرحله ساختار پرلیت تشکیل میشود. هیچ ناخالصی (آخال) بزرگی از سمنتیت در مرزهای فولاد هیپویوتکتوئید تشکیل نخواهد شد. در این موارد فرض این است که فرایند خنک سازی بسیار کند است و زمان کافی برای مهاجرت کربن را میدهد.
با افزایش سرعت خنکسازی، کربن زمان کمتری برای مهاجرت برای تشکیل کاربید در مرز دانهها خواهد داشت، اما مقادیر فزایندهای از پرلیت با ساختار ظریفتر و ریزتری در درون دانهها خواهد داشت؛ از این رو کاربید بهطور گستردهتری پخش میشود و از لغزش عیوب درون آن دانهها جلوگیری میکند که منجر به استحکامبخشی فولاد میشود.
در صورتی که سرعت خنک سازی بسیار بالا باشد، که بوسیله عملیات کوئنچ (quenching) انجام میشود، کربن زمان کافی برای مهاجرت ندارد، اما درون آستنیت (FCC) قفل شده و مارتنزیت را تشکیل میدهد. مارتنزیت یک فاز فوق اشباع کربن و آهن است که بسیار سخت اما شکننده است. بسته به میزان کربن، فاز مارتنزیتی اشکال مختلفی به خود میگیرد؛ زیر ۰٫۲٪ کربن، فرم کریستالی فریت (BCC) را به خود میگیرد، اما در درصدهای بالاتر کربن، ساختار (BCT) به خود میگیرد. هیچ انرژی فعال سازی حرارتی برای تبدیل آستنیت به مارتنزیت وجود ندارد، هیچ تغییری در ترکیب وجود ندارد و اتمها بهطور کلی همسایههای خود را حفظ میکنند
مارتنزیت، که در طول زمان سرد شدن منبسط میشود، چگالی کمتری نسبت به آستنیت دارد، در نتیجه تبدیل بین این دو منجر به تغییر حجم میشود که در این حالت خاص، انبساط روی میدهد. تنشهای داخلی ناشی از این انبساط عموماً به شکل فشردگی بر روی بلورهای مارتنزیت و کشش روی فریت باقی میماند و همچنین همراه با مقدار زیادی برش روی هر دو بخش است. اگر کوئنچ به درستی انجام نشود، تنشهای داخلی میتوانند باعث خرد شدن قطعههایی در هنگام سرد شدن شوند که این اتفاق موجب کار سختی داخلی و افزایش سایر عیوب میکروسکوپی میشود. هنگامی که فولاد با آب سرد یا همان کوئنچ میشود، ترکهای کوئنچ ایجاد میشوند، اگرچه ممکن است همیشه قابل مشاهده نباشند.
شرکت کانسار کاووش فولاد ایران یکی از بزرگترین شرکتهای صنعت فولاد با افزایش تعرفه های صادرات سنگ آهن توسط وزارت صنعت، معدن و تجارت، بازار داخلی رونق بیشتری پیدا کرده است. تامین کنندگانی که به معادن دسترسی دارند و میتوانند زنجیره تامین را تکمیل کنند، با تبدیل سنگ آهن خام به کنسانتره آهن، گندله آهن، آهن اسفنجی و در نهایت محصولات فولادی میتوانند سود زیادی کسب کنند.
شرکت ما به دلیل عقد قراردادهای طولانی مدت با برخی از معادن و روابط ویژه و اعتبار ایجاد شده طی سالیان با صاحبان معادن میتواند یکی از رهبران این حوزه جدید بازرگانی، به عنوان تامین کننده در کشور باشد.
بدون ديگاه